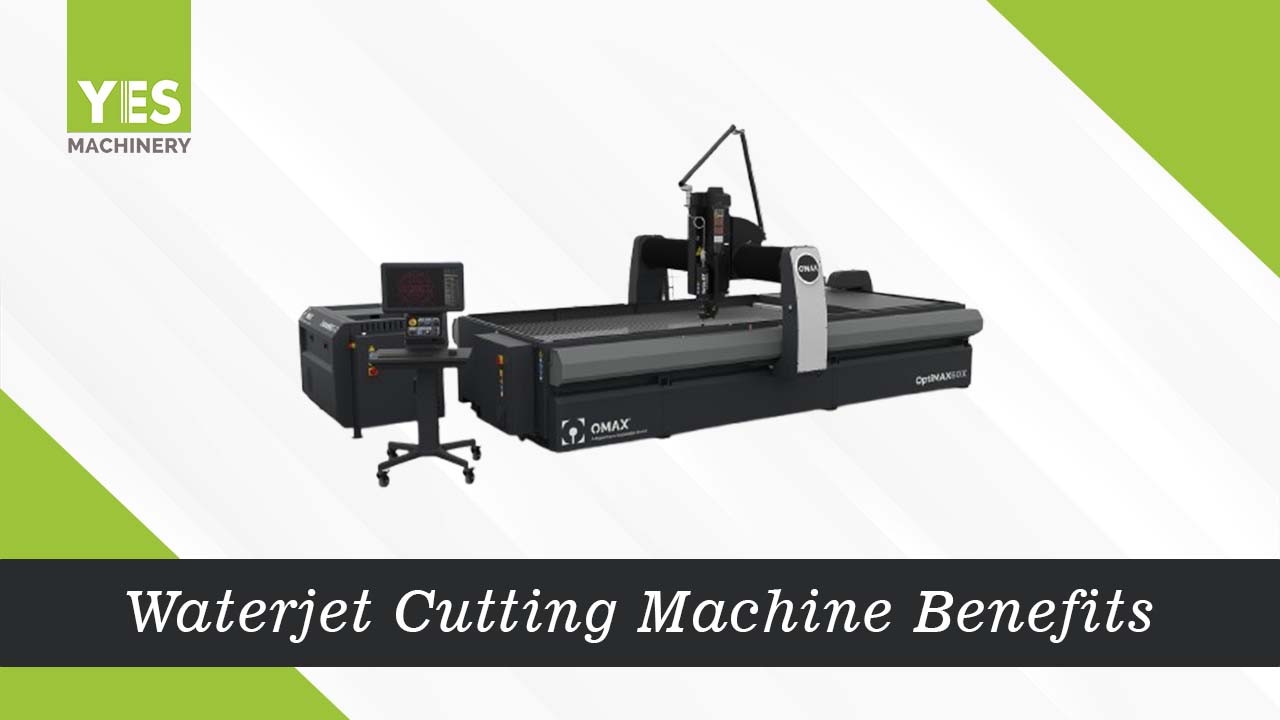
Top Benefits of Waterjet Cutting Machine
- Abrasive Waterjet Cutting
- Pure Waterjet Cutting
- Increased precision
- Little heat-affected region
- No tool changes requirements
- Affordability
- Compatibility
- Greatly sustainable
- Category Machines
The mechanical process where you can remove the materials through physical handling and material deterioration is termed as waterjet cutting. What makes waterjet cutting different from other forms of cutting is that it’s a non-thermal cutting process or cold cutting which means that there is no heat involved in the process.
All production processes are set to adhere to 3 core goals which are to enhance the production, lessen the wastage and build on the quality. The operations like three dimensional printing, injection moulding, plasma and laser cutting as well as sheet forming aim to accomplish the above goals at a lesser cost and reduced manufacturing time and at the same time aiming to enhance the efficiency and sustainability.
Each of these operations have their own position in the production industry because of the vast benefits as well as limitations. The advanced model waterjet cutters have included CNC technology in their configuration in order to meet the targets with good quality results.
Waterjet Cutting
A high-pressure jet of water in combination with an abrasive matter is made use of in waterjet cutting to cut a vast variety of materials. Pressure is applied on water using a high pressure water pump. This water is meant to pass through the high pressure tube to the cutting head. Inside the cutting head, the water will pass through a nozzle which will turn it into a perfect seamless stream. This stream is what cuts materials that’s placed before it.
Waterjet cutting machines are capable of generating pressure up to 100,000 psi which is equal to almost 6900 bars. To understand the magnitude of this pressure you can compare it with firehorses which usually offer pressures in the range of 8 to 20 bars. The vision system helps waterjet nozzles to easily offer precision and efficiency while cutting parts.
The nozzles of waterjet cutting machines can be handled very effortlessly in order to facilitate the cutting of materials of various kinds. Waterjet cutting is mainly classified into two based on whether or not an abrasive substance.
They are:
Abrasive Waterjet Cutting
During the process of cutting hard substances, usually abrasive agents are combined with water which takes place in a separate mixing chamber that’s situated in the cutting head which is just before where the abrasive jet gets exited from the system.
Some of the commonly used abrasive agents for waterjet cutting are garnet, suspended grit and aluminum oxide. With increase in material width/ hardness the use of abrasives also increases.
If you choose to use the right kind of abrasives, you can cut different types of materials. The materials that are most commonly cut with abrasives are stones, metals, plastics that are thick and ceramics. There are some exceptions like diamonds and tempered glass which are not possible to be cut with abrasive water. When you cut tempered glass with a waterjet you would find it shattering.
Pure Waterjet Cutting
Cutting materials without the use of abrasive by water jet cutters are called Pure waterjet cutting. Pure waterjet cutting is mainly used to cut soft materials. Since this cutter is designed only for cutting soft materials, it doesn’t come with a nozzle or a mixing chamber. The pressurised water is forced out from orifice with a high pressure pump thereby helping to create accurate cuts on the materials. Research has shown that most of the cutting machines used in industries employing waterjet technology will make use of both types.
In comparison to abrasive waterjet cutting, this method is less invasive. The jet stream is extremely fine and does not include any extra pressure on the jobpiece. This method of waterjet cutting is suitable for soft materials like felt, rubber, thin plastics, foam etc.
What are the benefits of waterjet cutting?
Waterjet cutting offers some benefits which makes it an ideal option for common as well as particular applications. Some of the advantages of waterjet cutting include:
Increased Precision
Well known for offering increased precision, the components of waterjet cutting machines are of premium quality even though they come with stringent specifications. Waterjet cutting machines are seen to perform their jobs offering tolerances up to 0.025mm which is equal to 0.001 inches. However tolerances in the range of 0.075 - 0.125mm are found to be very common for components which are lower than 1 inch thickness.
Based on the technology used, the tolerances can go up depending on how high the thickness of the materials. Factors like table stability, construction of machine, abrasive flow rates, cutting stream control, error in processing and lag in stream.
Little Heat - affected region
For the majority of the hot cutting procedures, heat affected zones are a byproduct. In laser cutting as well as EDM, the area around the edge where cutting is done would not melt during the machining process but would undergo change in its property.
Change in color, distortion in heat, edges hardened etc are found to influence the features of the final result. The final parts need heat treatment ahead of being put into usage.
Waterjet cutting being a cold cutting process does not create any heat affected zone. This offers the final results a premium quality and reliable features without putting any kind of stress on the result.
Using waterjet cutting thereby reduces the necessity of being concerned about imperfection in cuts, warping as well as any weak points. To reduce the production costs, manufacturers make use of pre-heated parts as well.
As waterjet cutting is a non-thermal process, there is little formation of slags and dross waste.
Premium Quality Parts
Waterjet cutting offers premium quality parts that’s unmatchable by other cutting methods. The final result offers parts that are seamless and hence do not require deburring. There are many factors that can contribute to the quality of the end result which includes pressure, size of nozzle, speed of cutting and abrasive flow rate. For best results, the parameters set during the process need to be adjusted.
Tool Changes
Waterjet cutters do not work with cutting tools and hence there is little requirement for nozzle changes which are done otherwise when materials of various types and thicknesses are used. In this cutting, the same nozzle can be made use of for various applications by changing the parameters of cutting stream like feed rate which helps in achieving the desired cutting speed.
Affordability
In comparison to other cutting methods specially in the Food Industry, waterjet cutting is found to be the most affordable. This method of cutting does not always require clamps, fixtures or jigs which helps in increasing the speed in other cutting processes.
Another major advantage of this curing technique is its possibility to pile and cut different material layers in one go. Piling can also be done for materials that are not similar which makes this the most easy and best method of enhancing the production parts.
Post processing is not required for any cut parts which will help in reducing the total cost. This process also helps in reducing the material waste.
Compatibility
As mentioned above, there is no restriction to the types of materials that can be cut by waterjet cutting method. A vast range of materials can be cut as long as the right parameters and abrasives are chosen.
Greatly Sustainable
In today’s age, sustainability plays a major role in choosing the type of production process. In terms of sustainability, waterjet cutting matches all the parameters required for being a sustainable process. Apart from not forming any slags, dross wastes or parts not getting hot, it does not generate any kind of toxic fumes.
Conclusion
Waterjet cutting comes with several advantages in comparison to other cutting methods. This cutting method is highly versatile and hence it can be used to cut any material while ensuring safety, sustainability and accuracy at the same time making it highly recommended in the majority of the industries.Waterjet cutting method find its application in aerospace, textile, manufacturing, mining, automobile as well as healthcare sectors. To find your best waterjet cutting machine in the Middle East, you can contact YES Machinery who holds the best brand from Europe in waterjet cutting machinery and service. YES Machinery has a well equipped team trained in waterjet cutting machines who are ready to offer you the best service upon your request.
Related Blogs
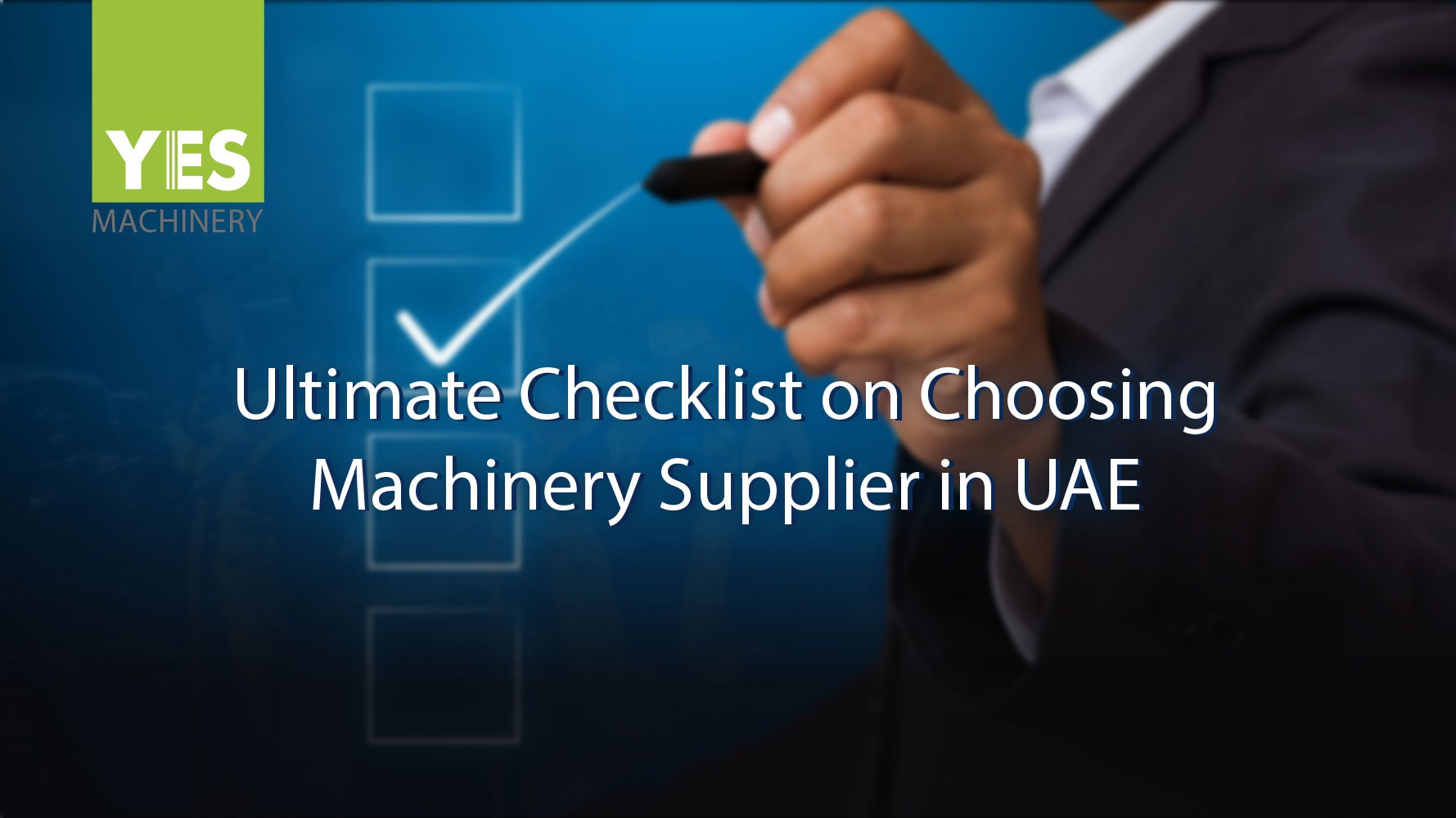
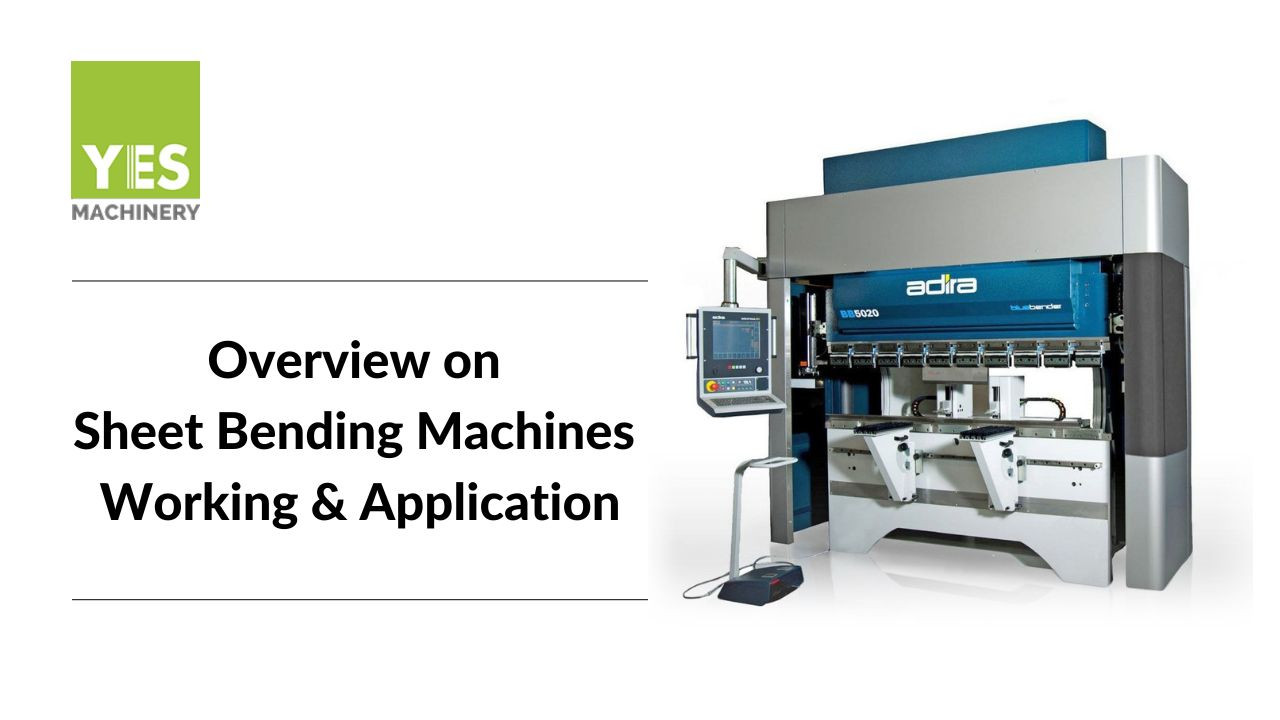
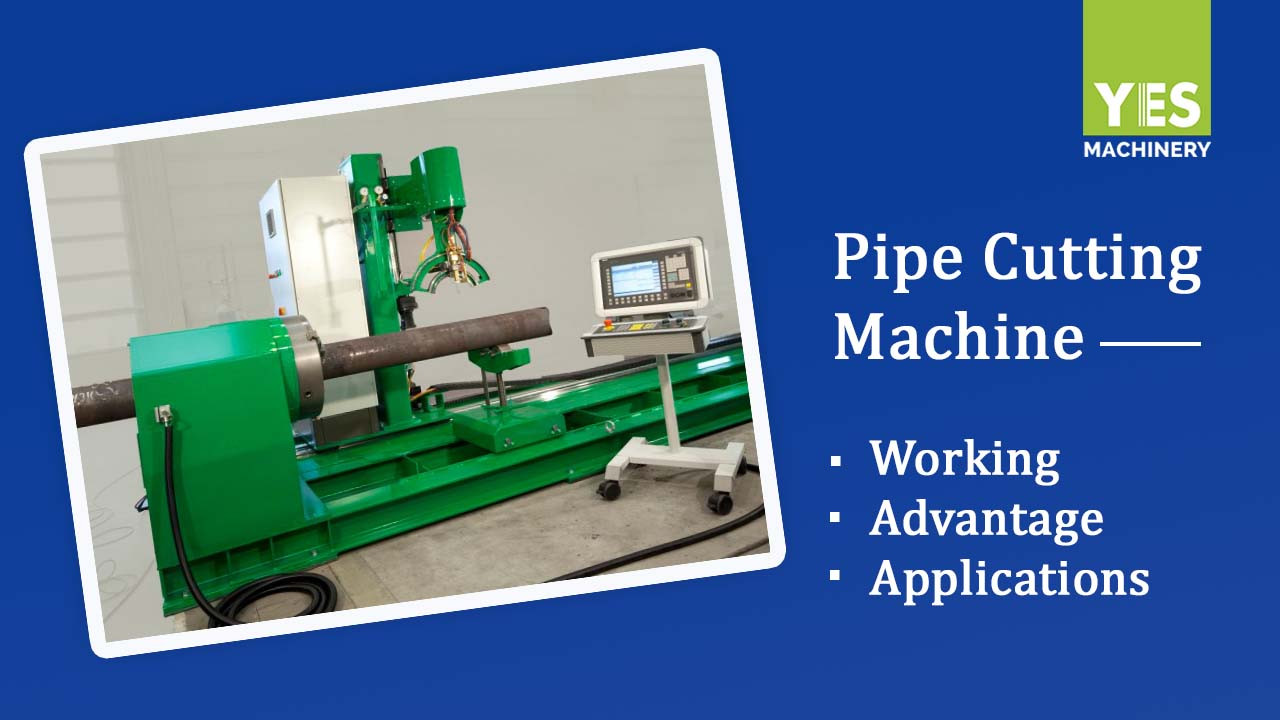
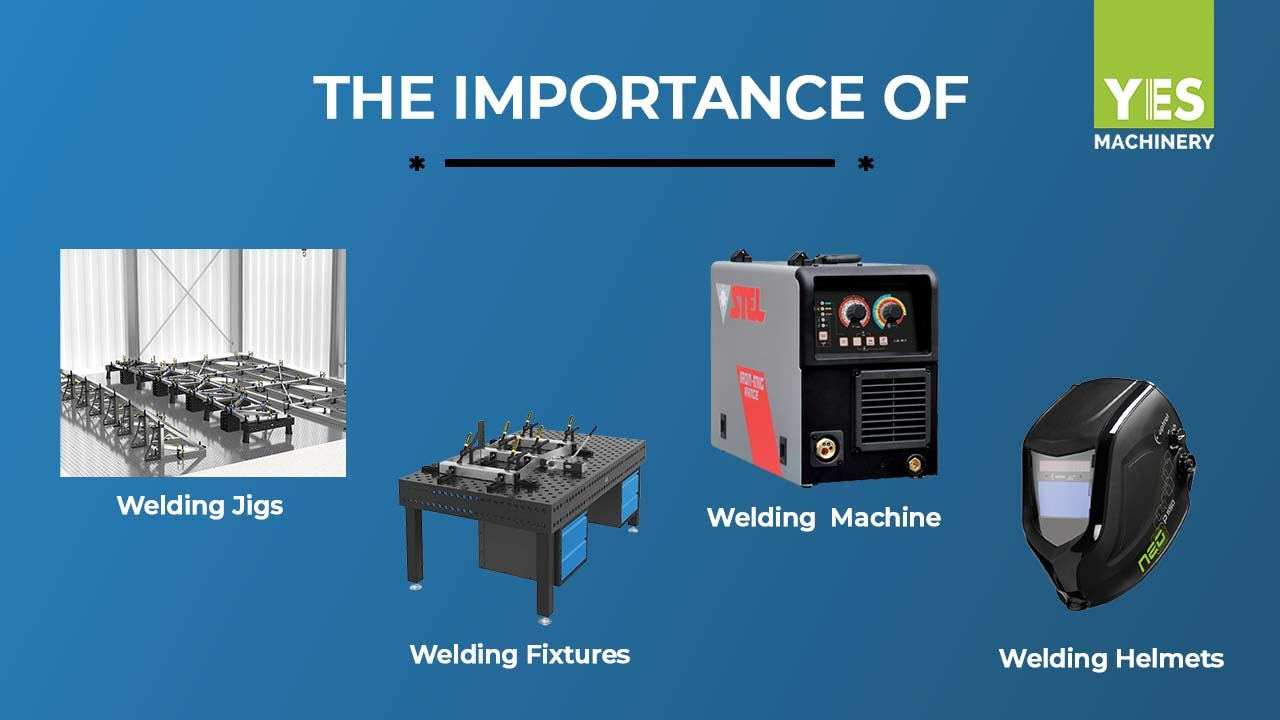
Search
Latest Blog
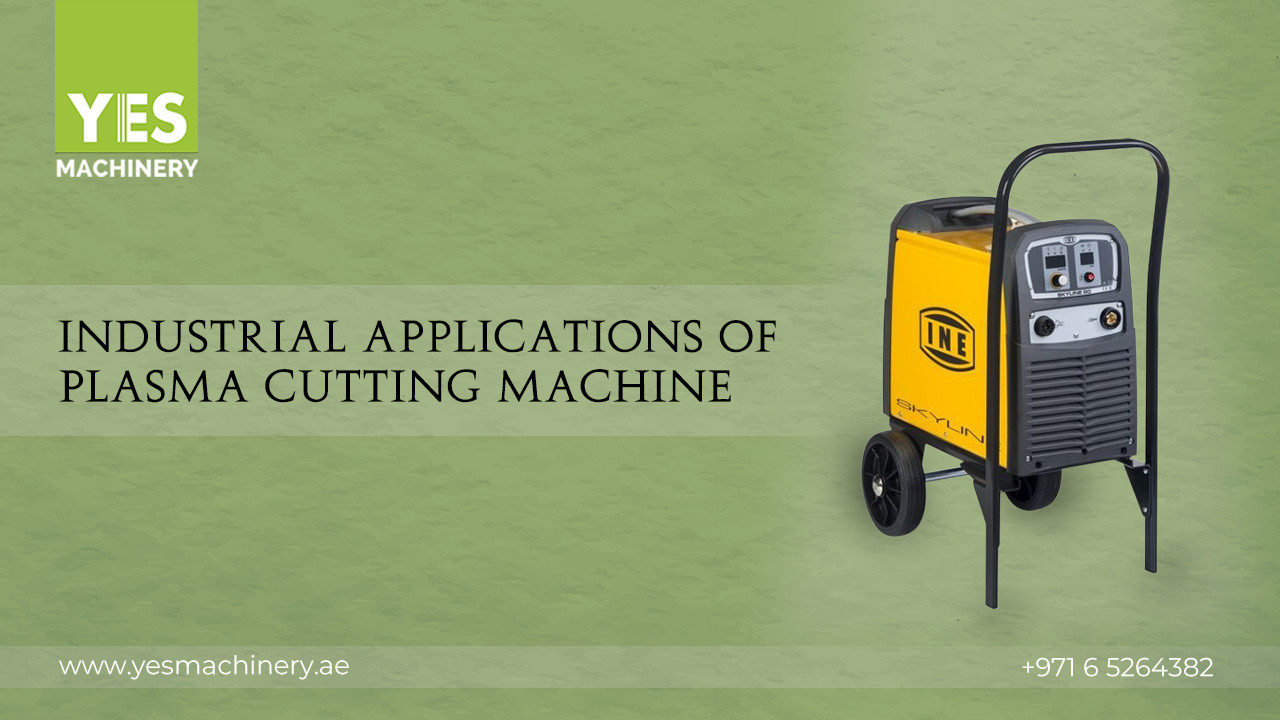
Industrial Applications of Plasma Cutting Machine
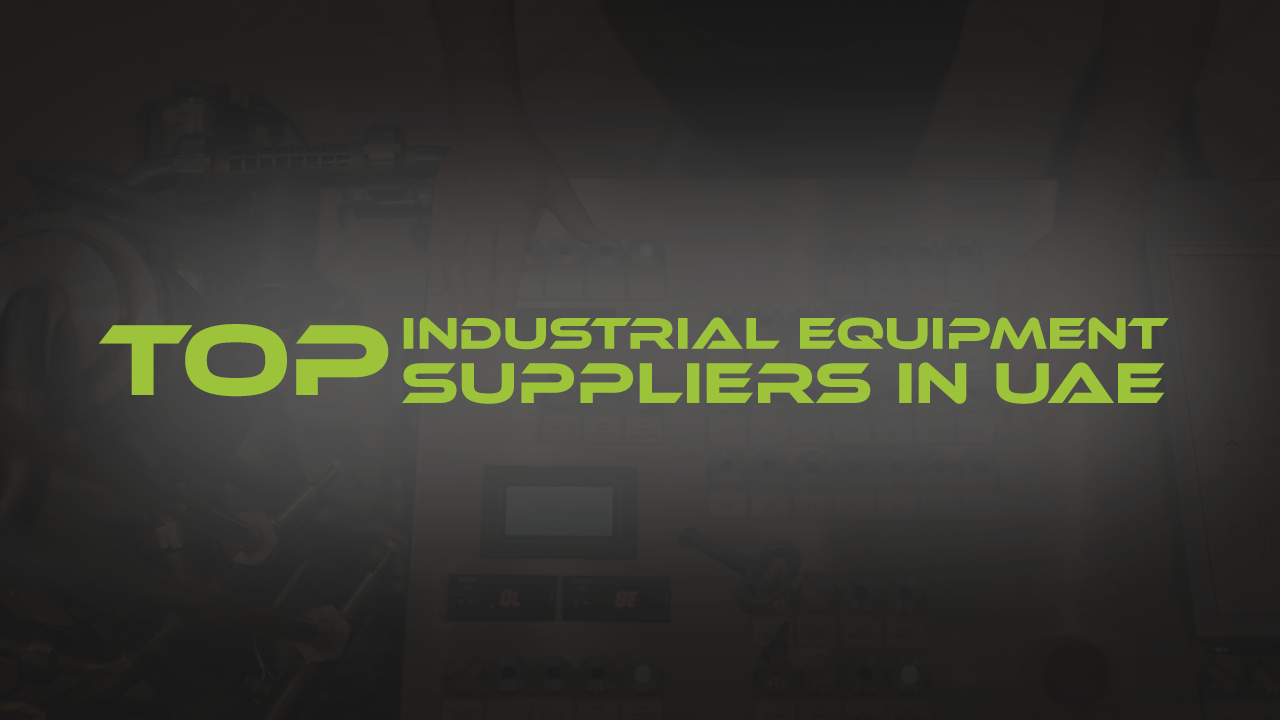
Top Industrial Equipment Suppliers in UAE
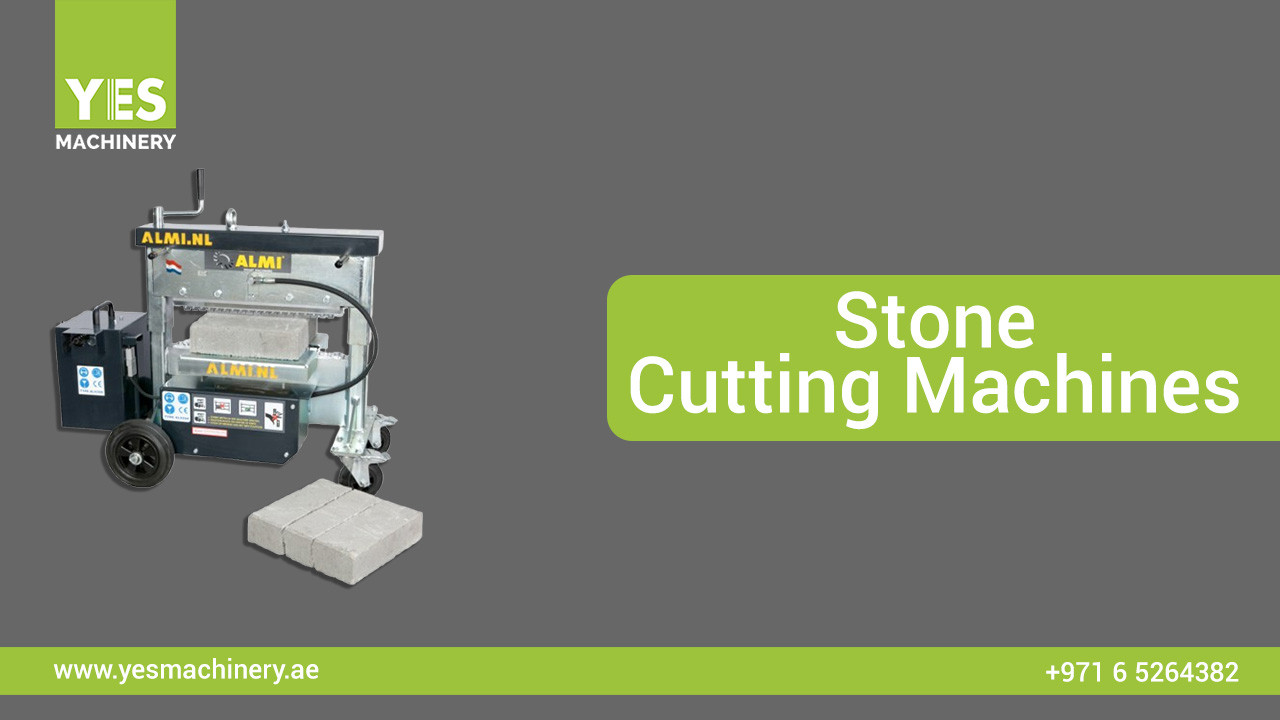
Key Advantages of Stone Cutting Machines
Categories
- Assembly and Lean
- Cleaning Machines
- Cleaning Robots
- Cutting, Notching, Punching
- Edge Preperation
- Grinding Machines
- Industrial Vacuum Cleaners
- Lifting
- Lifting and Manipulation
- Machines
- Marking Solutions
- Metal Forming
- Metal Joining and Fastening
- Packing
- Pipe Handling
- Storage Solutions
- Sweeper Tool Carrier
- Vacuum lifting machine
- Warehousing and Storage
- Welding