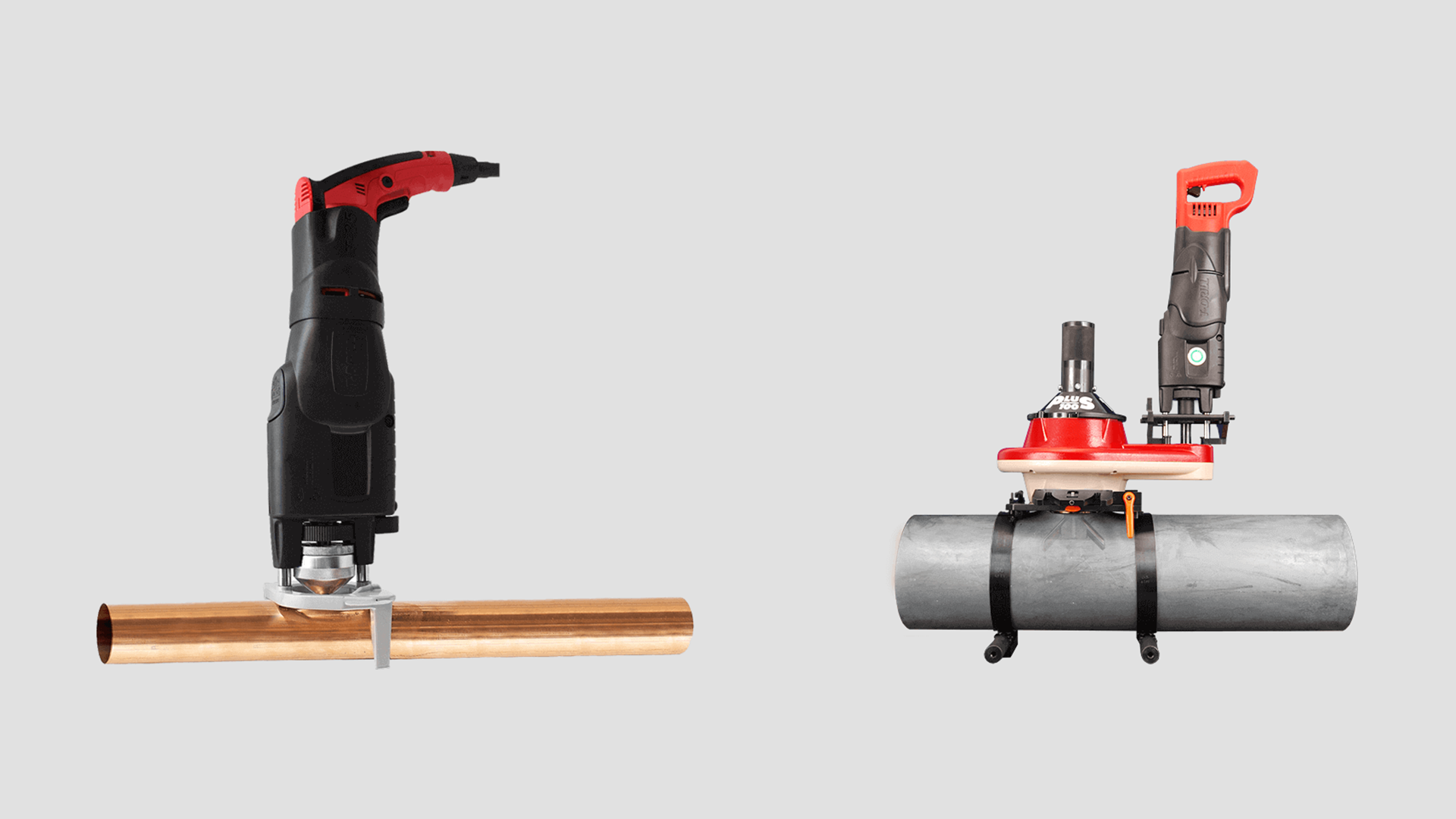
Are you looking to join two pipes
- No costly inventories
- Improved flow characteristics
- Instead of three welded joints, only one simple weld joint is required
- Remarkable faster through-put times
- Minimized inspection costless chance of leakage or call-backs
- Can be used in any malleable material
- Cut workshop costs by eliminating the need for welding and X-raying.
- Reduce the need for working capital: no welding neck flange inventory or complex welding and X-raying equipment is required
- Loose flanges save installation time by eliminating difficult bolt-hole positioning.
- Provide precise results and constant high quality: no risk of weld or braze fractures
- Capable of cold and hot forming both long and bent pipes with either smooth or grooved flanged surfaces.
- Programmability makes them very easy to operate and practically maintenance-free.
- Category Cutting, Notching, Punching
T-DRILL Collaring Method
Whenever two pipes need to be joined, T-DRILL is the answer.
Tee Forming – Pipe Branching – Collaring
The T-DRILL process is a patented method of producing outlets for branch connections. Pipe branching by T-DRILL method is also called collaring, mechanical tee forming or simple T-DRILL tees.
Butt welded joint is typically used in the process piping and heavier industrial applications. It provides a better quality inside surface, which is needed, where good flow characteristics and cleanliness are important. The T-DRILL collaring process is a method of producing outlets for branch connections directly from the run material. The process from hole cutting to collar trimming is carried out in a single workstation in one set-up from outside the pipe and no access into the pipe is needed from the end of the
First an elliptical hole is milled in the pipe. Since more material is needed in the “stirrup” area to get a good collar height for butt welding, an elliptical hole is used as a pilot hole rather than a round hole, which is used in the lap joint. After the pilot hole is made, the forming pins of the collaring head are extended, and the collar is formed. This is aided by automated lubrication and optimized forming. Then the collar is trimmed to the desired height and the branch pipe is connected to the run pipe by butt welding.
Tube Flanging
Flanging eliminates the need for welding since the flange is mounted loosely behind the formed end configuration!
T-DRILL Flanging Machines form a lip or flange directly on the end of the pipe allowing the use of loose flanges. This process saves up to 40 % of the time compared to traditional weld neck flange connections. The flange – also called the Van Stone and loose flange – is achieved by roll forming a flange on the end of the pipe spool. The flange can have a smooth or grooved face, depending on the forming (rolling) tool used.
A loose commercial flange backs up the formed pipe end; when the connection is made, a gasket is sandwiched between the two formed flanges, held together by the bolted commercial flanges. Since the flanges are loose, they eliminate welding and allow free rotation for alignment and bolt-up, providing so a significant cost reduction.
Both the process in tandem saves the time, costs and enhance productivity as compared to a traditional welded fitting. For illustrative purpose, we will do a comparison between traditional welded fittings and T drill Collaring & Flanging.
COMPARISON: Welded Fittings vs T-DRILL Collaring & Flanging
Traditional Orbital Weld fittings for above process involves steps costing time, labor and money. A typical process as above requires 6 fittings, 5 pieces of pipe and 10 Weld joints to form the typical shape. The operator must cut the pipes, polish the same, do tack welding and then orbital welding of joining flange part to the branch and main pipe. For the complete fabrication process, it involves 7 hours and 20 minutes of labor work which is tried, tested, and documented by T Drill. That means almost a days work.
Whereas
T-DRILL Collaring & Flanging + Orbital Welding process for the same job requires only 3 Pieces of Pipe and 2 Weld Joints for the complete joining. With 2 process we achieve faster result, i.e., Collaring of the tubes and flanging of the pipes at the end. No need for separate fittings for pipe and flange part and then the process of welding the same at the end. We can achieve the flanging in the same pipe with T Drill flanging machines. It can save time even 98 % and total cost more than 50 % compared to traditional welding method. The result is always precise and stable flange without welding seam, meaning that the X-ray inspection is not needed. And the whole process gets completed in 1 hour 5 mins which means its almost 6 times faster than the traditional process and the no. of steps for processing and parts used are minimal. That means less cost, less man hours, less weld joints and faster productivity.
Typical applications areas are in food processing, pharmaceutical, pulp and paper industry, stainless steel piping systems, water treatment, shipbuilding, conventual and nuclear submarines.
ADVANTAGES:
Related Blogs

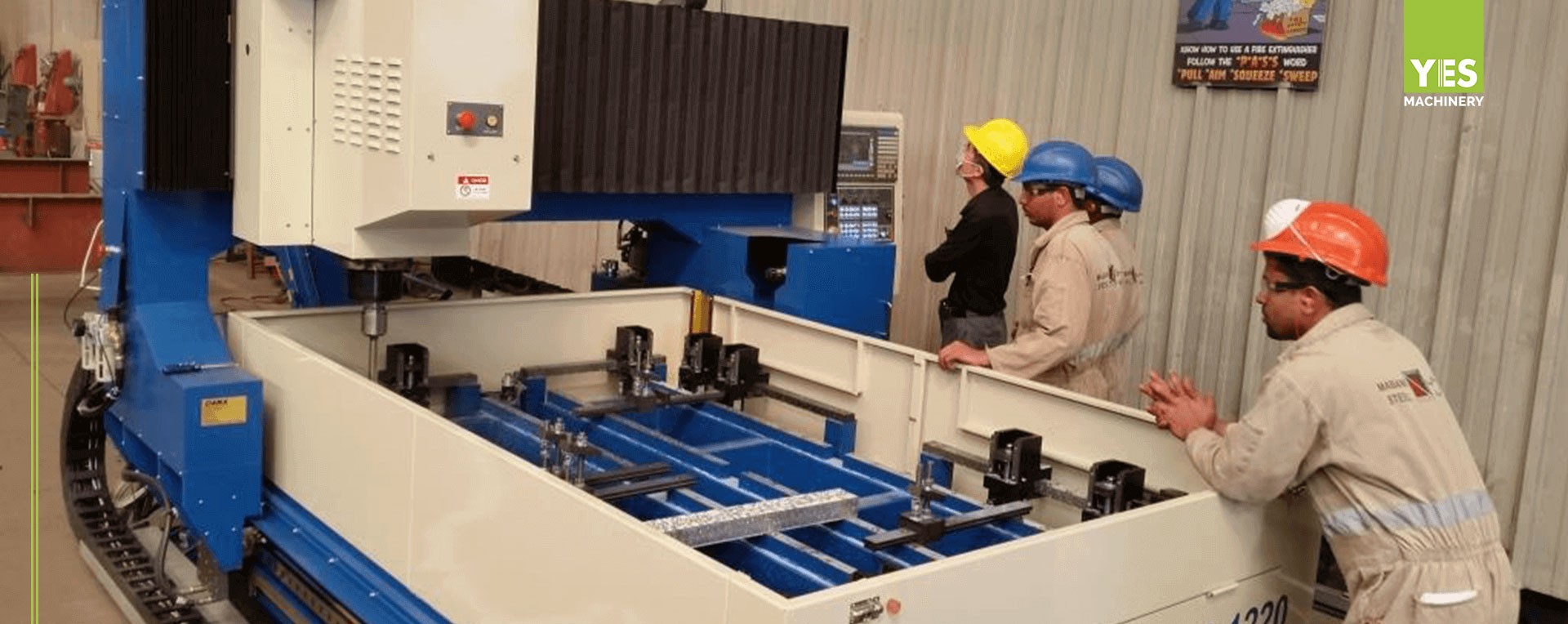
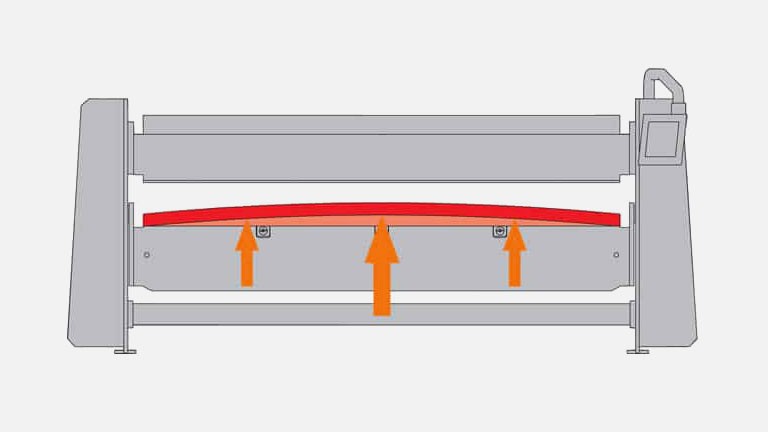
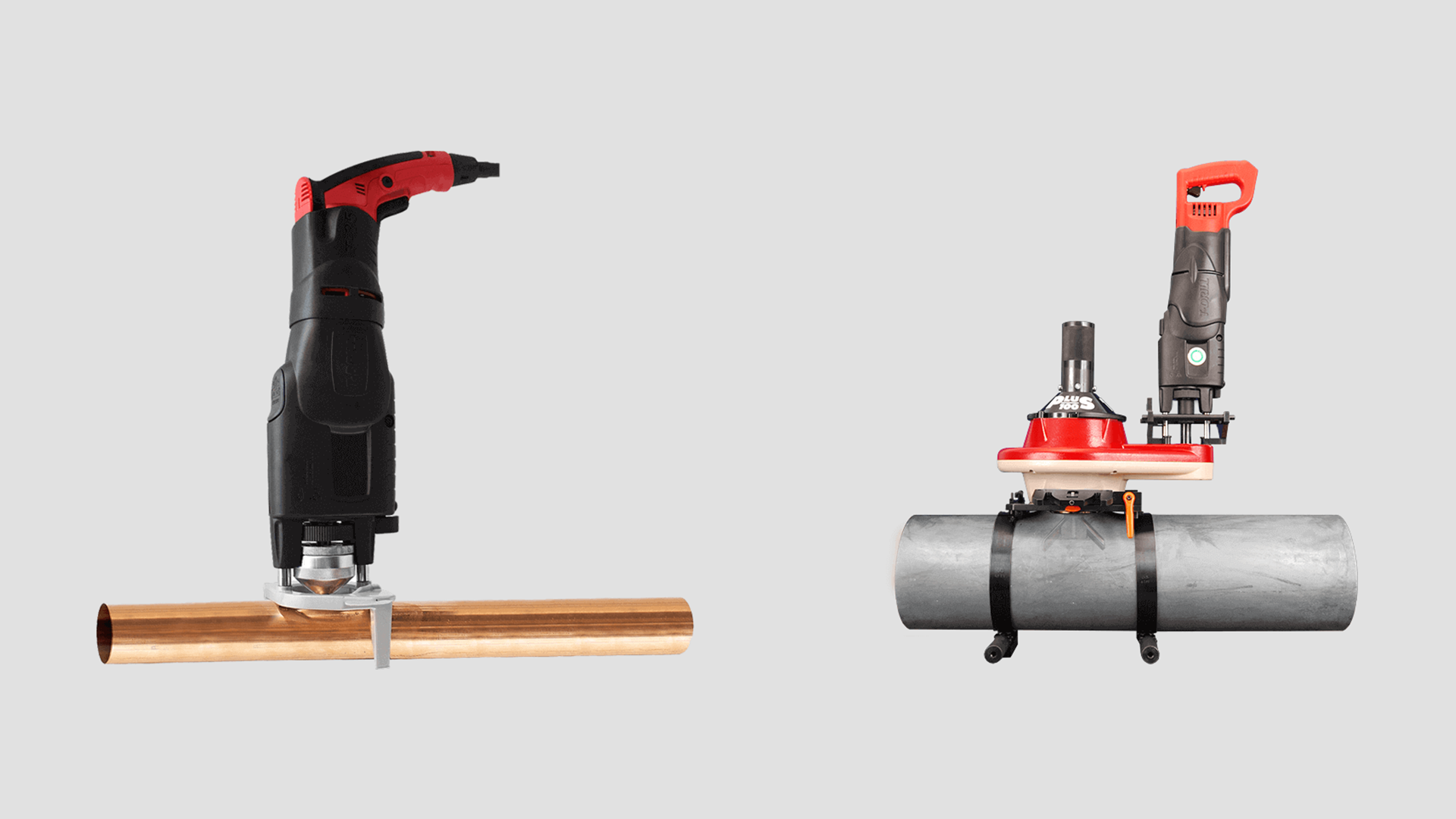
Search
Latest Blog
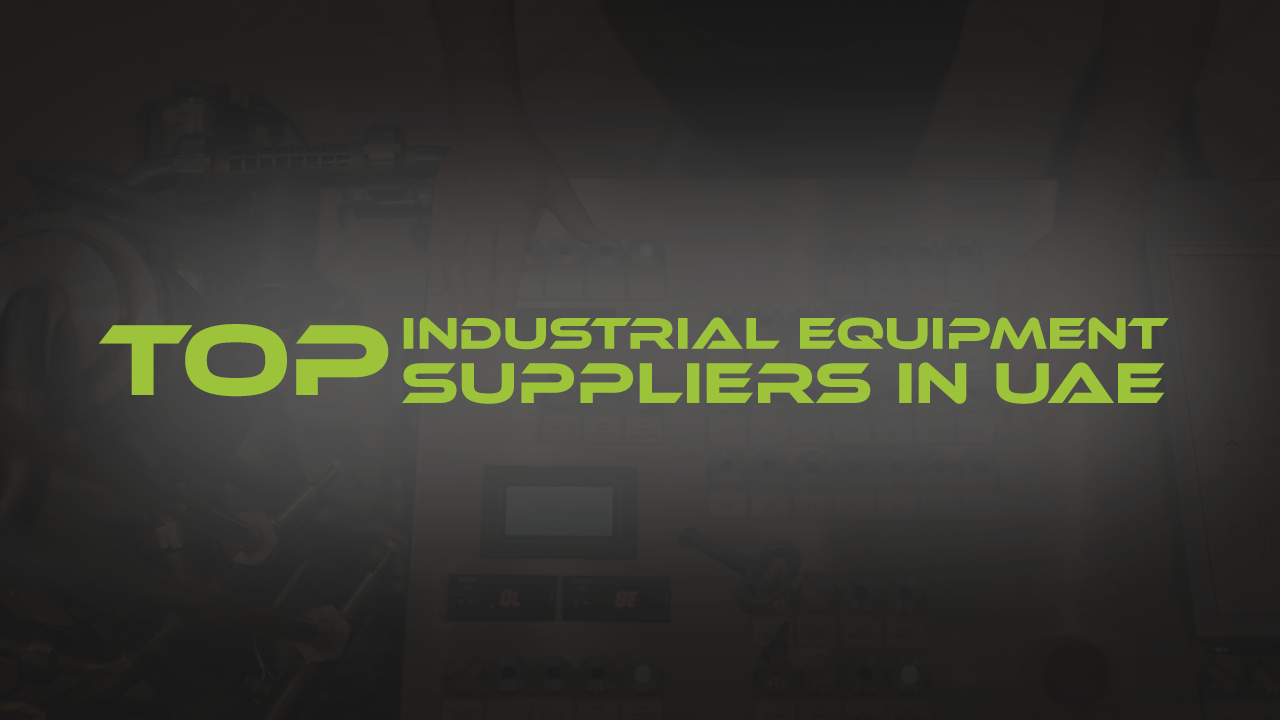
Top Industrial Equipment Suppliers in UAE
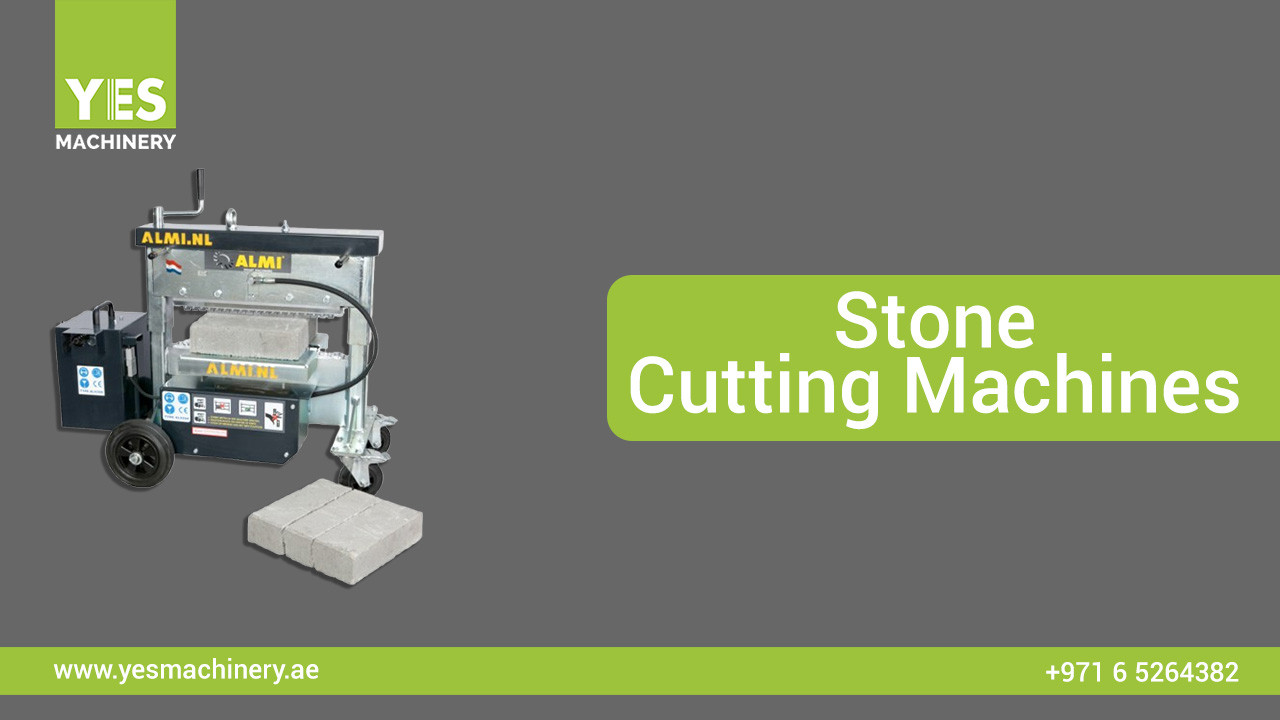
Key Advantages of Stone Cutting Machines
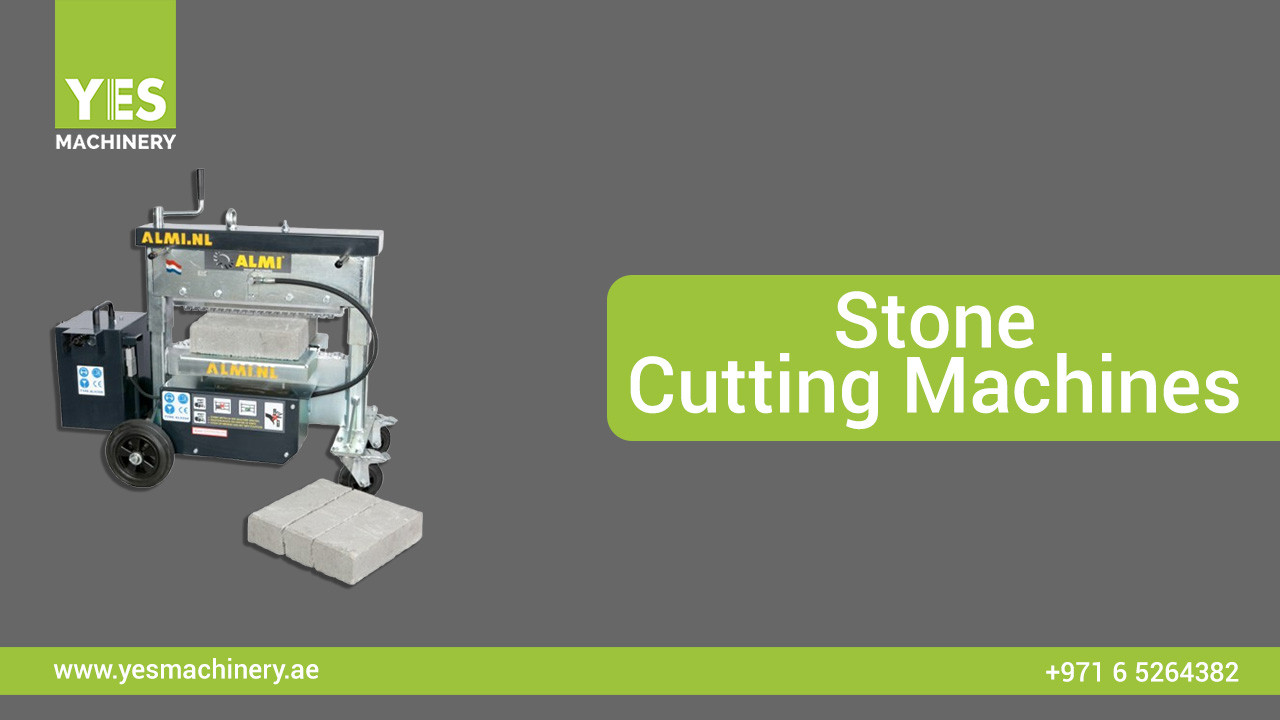
Detailed Overview on Stone Cutting Machines
Categories
- Assembly and Lean
- Cleaning Machines
- Cleaning Robots
- Cutting, Notching, Punching
- Edge Preperation
- Grinding Machines
- Industrial Vacuum Cleaners
- Lifting
- Lifting and Manipulation
- Machines
- Marking Solutions
- Metal Forming
- Metal Joining and Fastening
- Packing
- Pipe Handling
- Storage Solutions
- Sweeper Tool Carrier
- Vacuum lifting machine
- Warehousing and Storage
- Welding