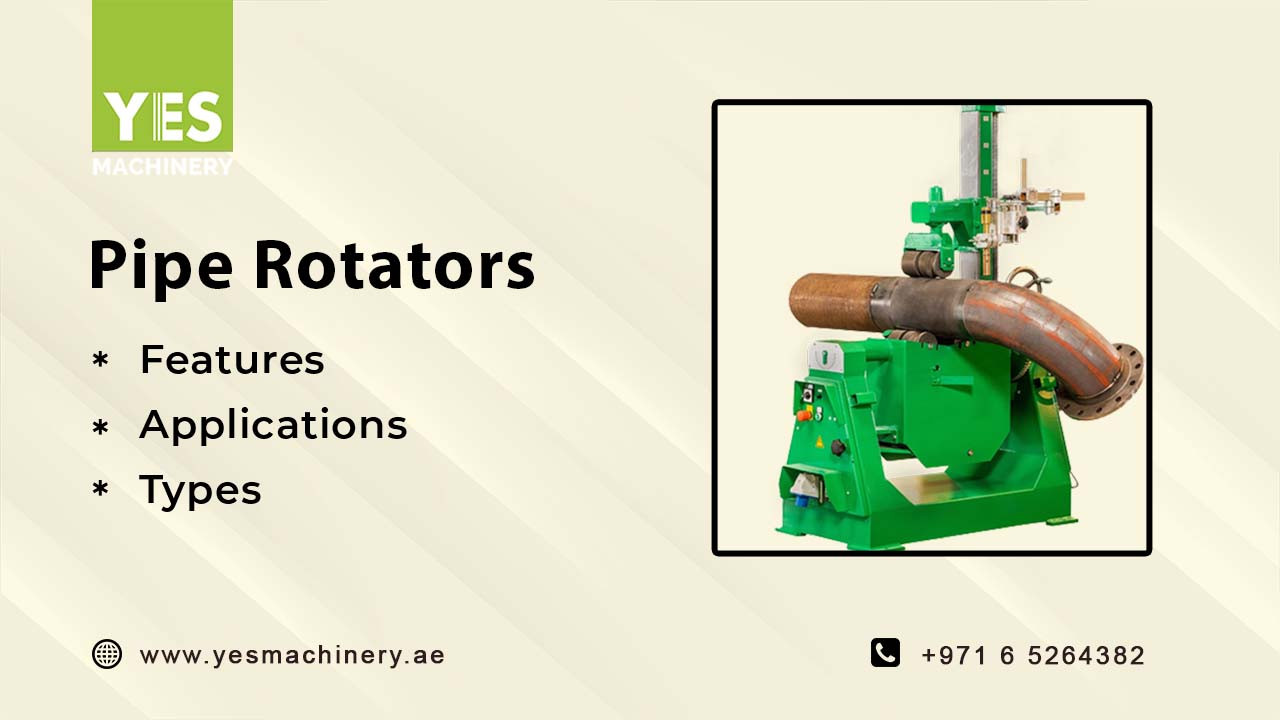
Pipe Rotators: Features, Applications and Types
- Category Pipe Handling
Pipe Rotators
A pipe rotator, also known as a welding rotator, is typically used for pipes. They are also referred to by many as the same products. It's critical to comprehend the fundamentals of various pipe rotators if you intend to purchase and use one for your own business. This is a succinct yet comprehensive explanation to provide you with an understanding of the numerous facets of pipe rotators.
Basics of a Pipe Rotator
Pipe rotators are used to weld cylindrical and round objects. Pipes, API pipes, heat exchangers, mounted vessels, wind turbines, boilers, LPC bullets, barrels, pressure vessels, and tanks are some of these items. Pipe rotators are used in both light and heavy fabrication facilities to position and rotate circular objects. Heavy housings don't need to be manually rotated by welders because Pipe Rotators do it for them.
Calibers and supported load ranges are the primary factors that separate various Pipe Rotators. Strength and strength speeds are further features, as well as wheel and surface components. Pipe Rotators are arranged in sets, one of which has double rollers, one of which has an electrical engine turning it. An aid in accomplishing this is a reduction gearbox. These are arranged so that different caliber cylinders can fit in the space between the rolls.
They are set up in a made-up case with a basic form. On the shop floor, two of these cases need to be placed apart from one another. The cylindrical housings that need welding are held in place by this. Uncertainties that could cause the workpiece to reverse require further thought. Small positioning errors may cause the workpiece to be rendered along its axis.
Pipe rotators that are not square or parallel may produce drag forces that cause the workpiece to be pushed uncertainty. Steel, rubber, and polyurethane are additional materials included with pipe rotators.
Features of Pipe Rotators
Due to a number of characteristics, pipe rotators have supplanted conventional welding methods.
• Pipe Rotators support stationary cylindrical housings as well as rotating pipes and tanks.
• Pipe rotators can load a ton of material. The weight capacities range from 3000 pounds to more than 2 million pounds.
• Pipe rotators have a variety of dynamic composite wheels. Their use potential is greatly increased by this trait.
• Rotators for pipes have precise center distances. They are able to produce accurate outcomes as a result.
• The chassis design of Pipe Rotators is effective and efficient. This makes them sturdy and long-lasting.
• Overload discs on pipe rotators protect rubber tires weighing more than 5000 lbs.
Pipe Rotator – Benefits
Pipe Rotators make significant time, cost, and effort savings. In addition to structural advantages, they also have operational advantages. The principal structural advantages include:
• Rotators for pipes are quite strong. They are designed to support hefty objects.
• Pipe Rotators are quite portable. They are easily movable and adjusted.
• Pipe Rotators have a small overall footprint. Their parts are arranged in a tidy package.
• They are simple to use and alter.
• The structural rigidity of pipe rotators is inherent that lasts a long duration.
• Pipe Rotators can provide the huge diameter that low pressure parts require.
They reduce the amount of labor required while improving productivity and precision when welding pipes and other cylindrical housings. Their user benefits can be summed up as follows:
• The usage of pipe rotators ensures the security of the rotator housings and the operator.
• Pipe Rotators are renowned for delivering accurate and dependable results.
• Pipe rotators are highly effective at carrying out consecutive tasks.
• Utilizing a pipe rotator increases production.
• Pipe rotators are more practical and cost-effective since they reduce operating expenses.
• One of the main advantages of pipe rotators is the amount of time they can save working. They are in charge of shorter operation times.
• Pipe Rotators can swiftly and efficiently join numerous rounded and cylindrical housings.
Which welding processes are supported by pipe rotators?
In intricate assemblies and circumferential welding procedures, pipe rotators can be used. They include Sub Arc Welding, Tungsten Inert Gas welding and Metal Inert Gas welding.
Parts of a Pipe Rotator
Welding Rotators are compactly made and designed. Their components are arranged in a tidy package. This design makes it simple and efficient for the workers to operate and alter the pipe rotators. The pipe rotators consist of five key components. They can't be removed because they are built in. The various parts are:
• Idler
• Driving Wheels
• Wheel Frames
• Transmission Device
• Controller Direct Current Motor
Types of Pipe Rotators
Depending on the use and the unique requirements of the customer, there are various types of pipe rotators. There are essentially two types of pipe rotators.
Self – Aligning Pipe Rotators
Pipe rotators that self-align take care of the positioned rotator objects. They accept any object calibers that fall within a certain range. This machine is utilized to adapt to the differences in shell diameter between various objects. To ensure a steady pace, these rotators are powered by either a DC or AC motor. They are suitable for:
• a cutting-edge creep control tool with a plus or minus 5 creep range
• The grab shock loads are attached by a high-stress rubber cushion, preventing gearbox damage.
• a disc to prevent potential tire damage.
Conventional Pipe Rotators
An idler supporting unit and a motorized driving unit make up a conventional welding rotator. A powerful DC or AC motor that is built to rigorous international specifications to ensure constant speed with a 15% external balance load powers the power unit. To absorb shock loads and prevent gearbox damage, the heavy-duty tires are constructed with high stress rubber cushion mounts with a 65-degree lasting hardness.
Other characteristics are:
• Gauges for oil's light level
• When raising center weights, skid structural security will minimize any deterioration on the control box.
• Plus, or minus 5 vessel creep management is possible thanks to an anti-creep device feature.
• Disc overload to prevent any potential tire damage.
Where are Pipe Rotators Used Most Commonly?
Most of the ordinary items we use involve welding. We are surrounded by many things made by various welding procedures, ranging from autos to mobile phones. More than 30 different welding techniques exist. Additionally, a variety of machines support welders in their unique work requirements.
The major industries that make use of welding rotators are:
• Automotive Industry
• Construction and Infrastructure Industry
• Manufacturing Industry
• Railroads
• Shipping Industry
• Aerospace Industry
Where can I buy Pipe Rotators from?
There are so many pipe rotators on the market that picking the ideal one for your particular use might be challenging. The strongest and most precise pipe rotators on the market are sold and supplied by YES Machinery in the UAE. They make sure to deliver you the greatest quality for the best experience and have the top brand from Germany.
Related Blogs
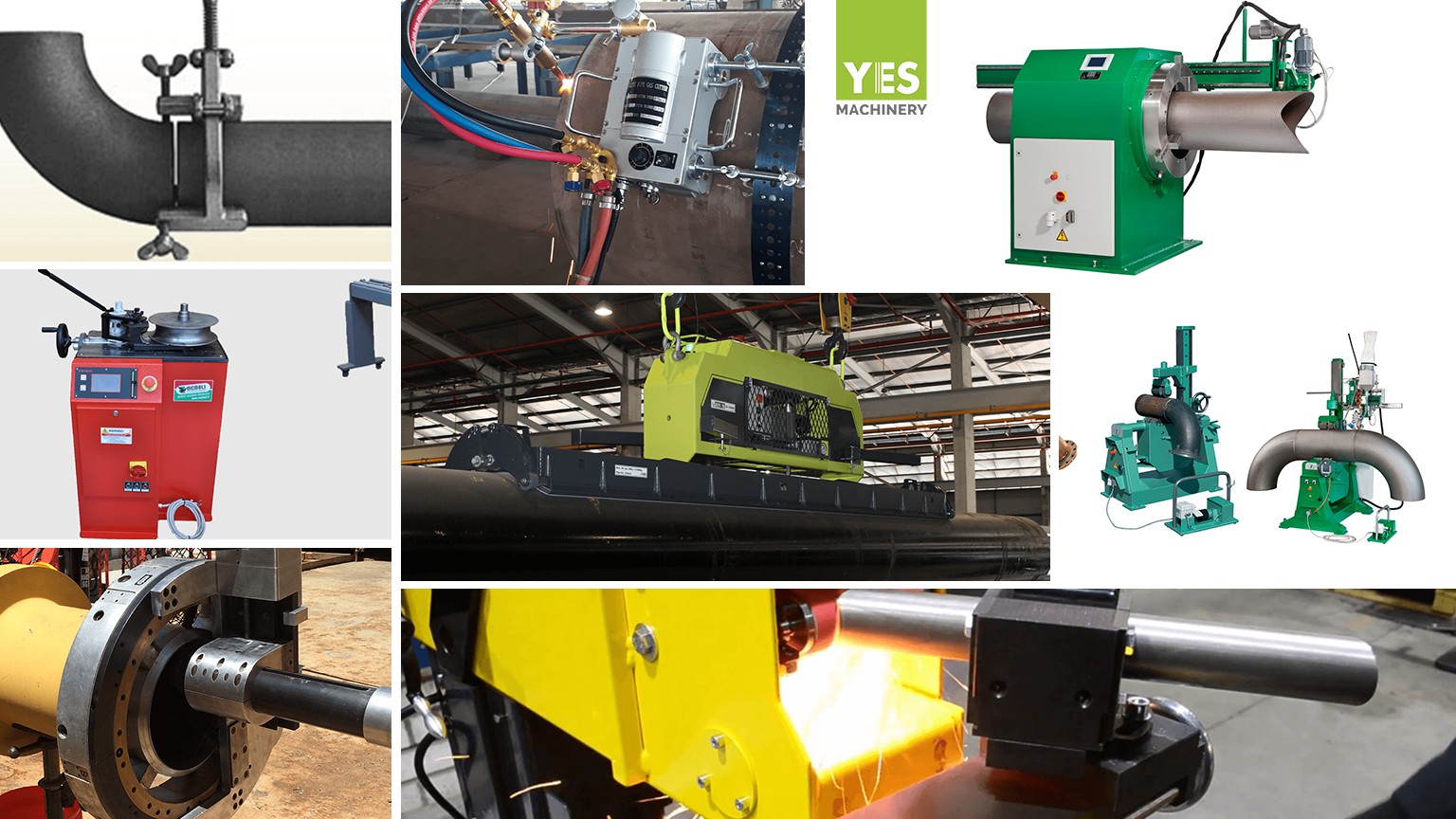
Search
Latest Blog
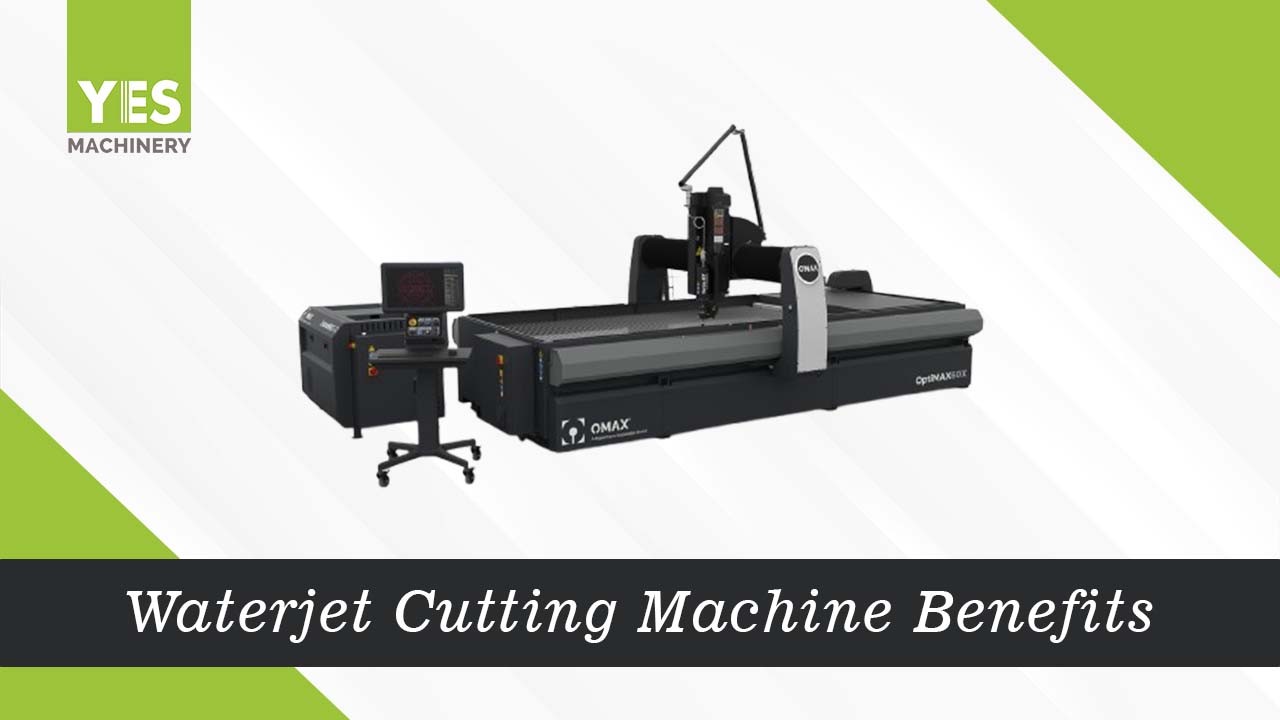
Top Benefits of Waterjet Cutting Machine
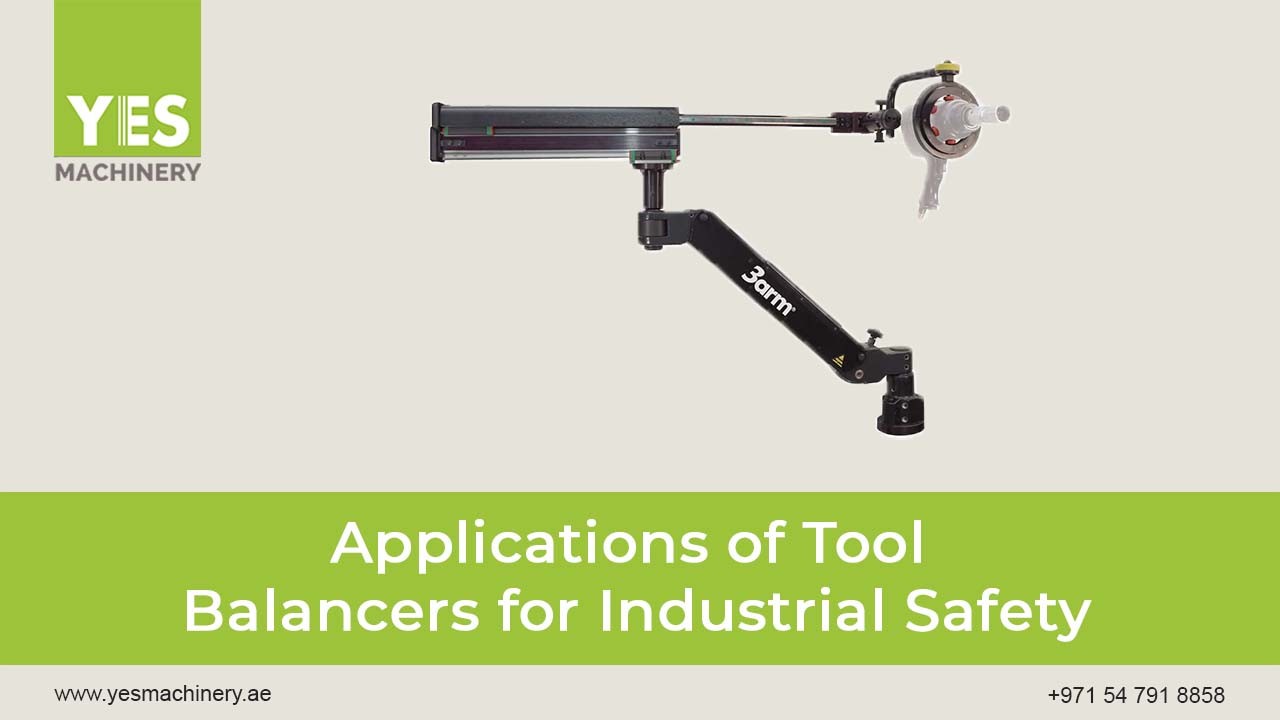
Applications of Tool Balancers for Industrial Safety
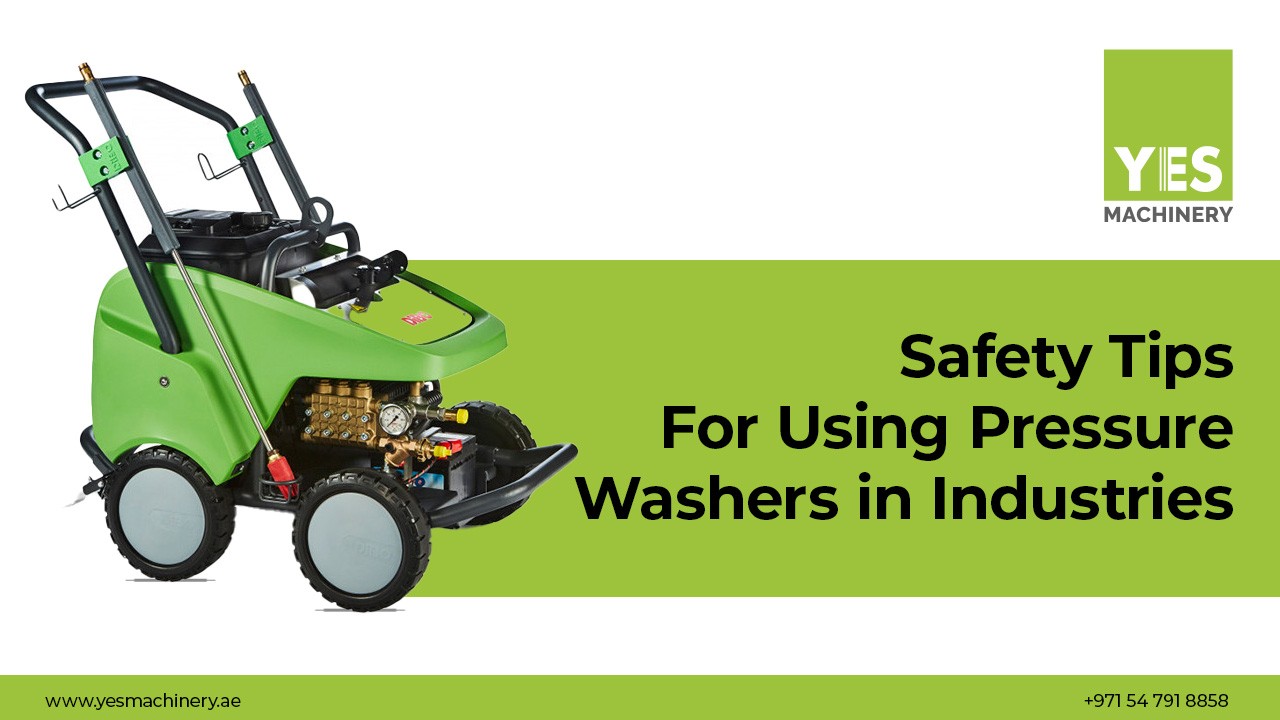
Safety Tips for Using Pressure Washers in Industries
Categories
- Assembly and Lean
- Cleaning Machines
- Cleaning Robots
- Cutting, Notching, Punching
- Edge Preperation
- Grinding Machines
- Industrial Vacuum Cleaners
- Lifting
- Lifting and Manipulation
- Machines
- Marking Solutions
- Metal Forming
- Metal Joining and Fastening
- Packing
- Pipe Handling
- Storage Solutions
- Sweeper Tool Carrier
- Vacuum lifting machine
- Warehousing and Storage
- Welding